
Stady state and Transient Thermal analysis of an Aluminum Heat Sink with consideration of thermal stress.
Problem Statement
The problem involves conducting a thermal analysis of an aluminum heat sink under various conditions, including steady-state and transient scenarios, as well as considering thermal stress.
- Material properties: The heat sink is made of aluminum with specific thermal conductivity (k), density (ρ), specific heat (c), Young’s modulus (E), Poisson’s ratio (ν), and thermal expansion coefficient (α).
A fan forces air over all surfaces of the heat sink except the base, where a prescribed heat flux (q′) is applied. The surrounding air temperature and heat transfer coefficient (h) are given.
Analysis Approach
Utilizing the given material and boundary conditions, the problem involves solving for temperature distribution within the heat sink over time, considering both steady-state and transient conditions. Additionally, the thermal stress response due to fixed base conditions is examined using the steady-state solution as a temperature load.
Timeframe: The transient analysis is conducted over a period of 180 seconds, with the square wave function having a period of 90 seconds and transitioning between 0 and 1000 W/m².
Methodology: Solutions are obtained through Analytical calculations and numerical simulations, likely involving finite element analysis or similar techniques to account for complex thermal and mechanical interactions within the heat sink.
Material Properties
Density ρ = 2800 kg/m3
Specific heat (c) = 870 J/(kg K)
Young’s modulus E = 70 GPa
Poisson’s ratio ν = 0.3
Thermal expansion coefficient α = 22 × 10−6 /°C
Geometry
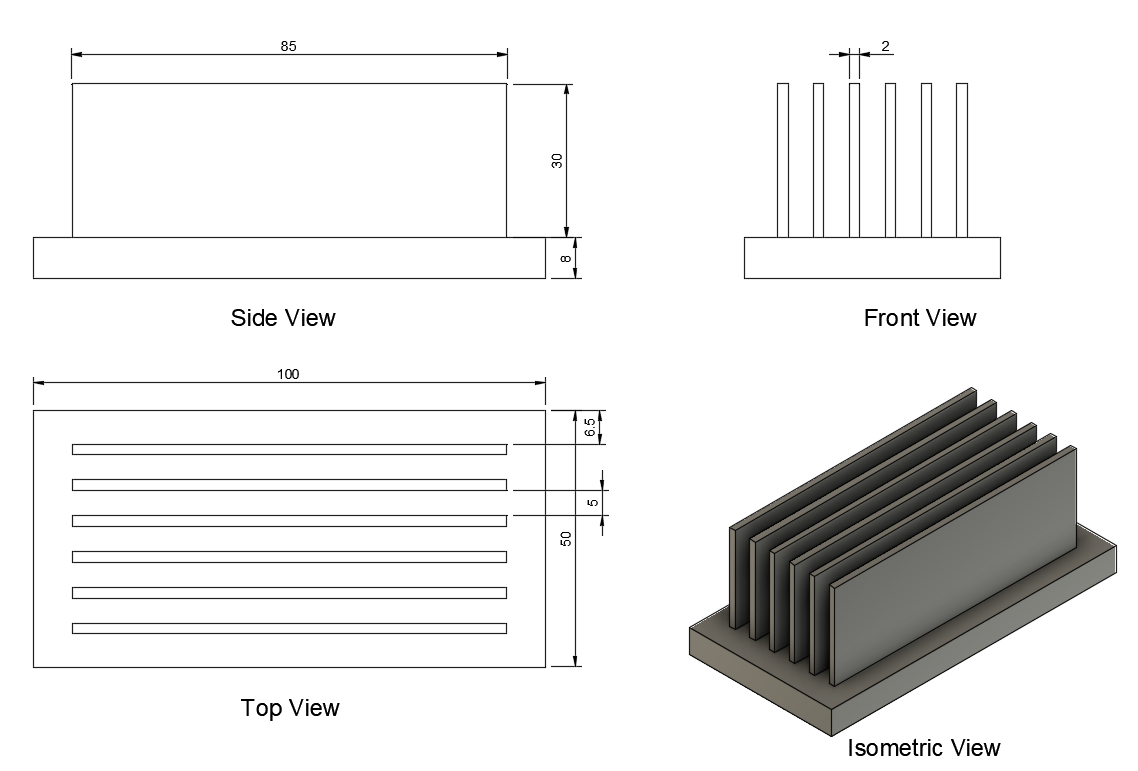
Generated Mesh
Total Elements: 1267541
Total Nodes: 5326732
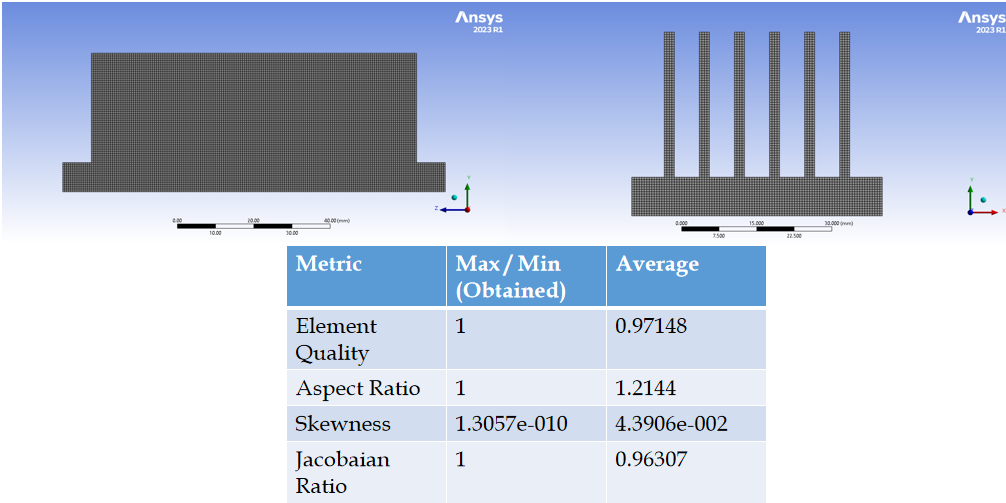
Force Calculations
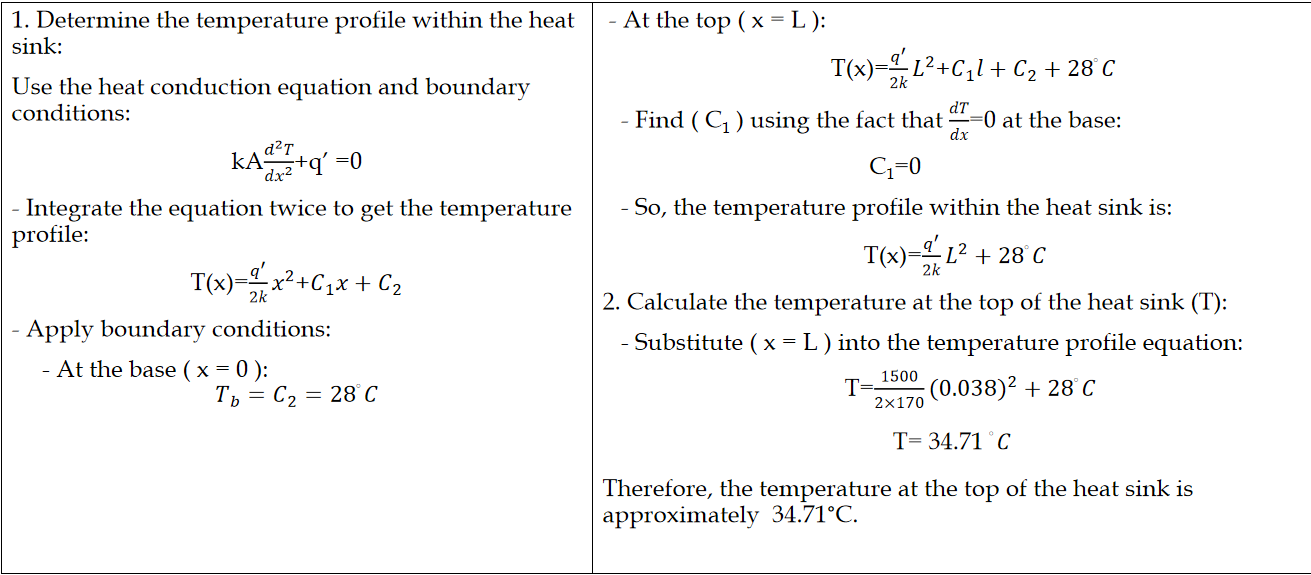
Task-1: Steady State Thermal Response
Problem, Boundary conditions and Initial conditions
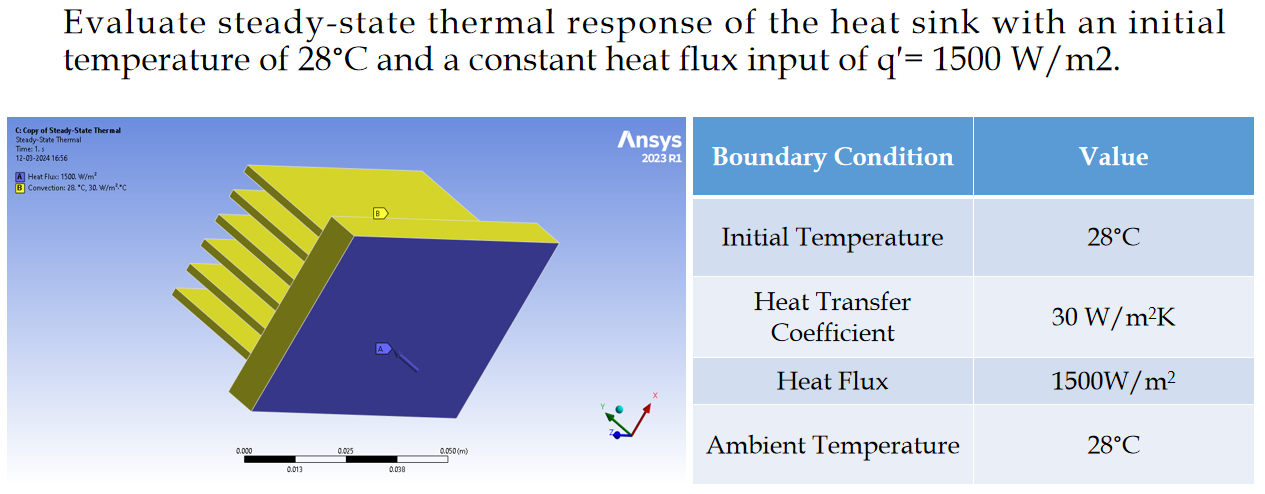
Results
Minimum Temperature: 34.19°C
Maximum Temperature: 34.917°C
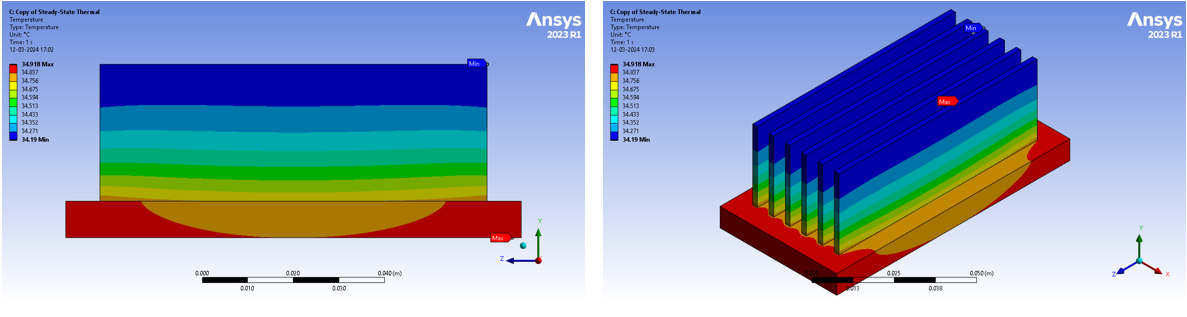
Conclusion
Efficient heat dissipation achieved due to high thermal conductivity (k = 170 W/(m K)) of aluminum heat sink.
Stable temperature gradient maintained from base to fins, ensuring uniform cooling of electronic device.
Steady-state condition essential for reliable operation and prolonged lifespan of electronic components.
Delta T observed analytical is same as that observed in CFD results.
Task-2: Transient Thermal Response
Problem, Boundary conditions and Initial conditions
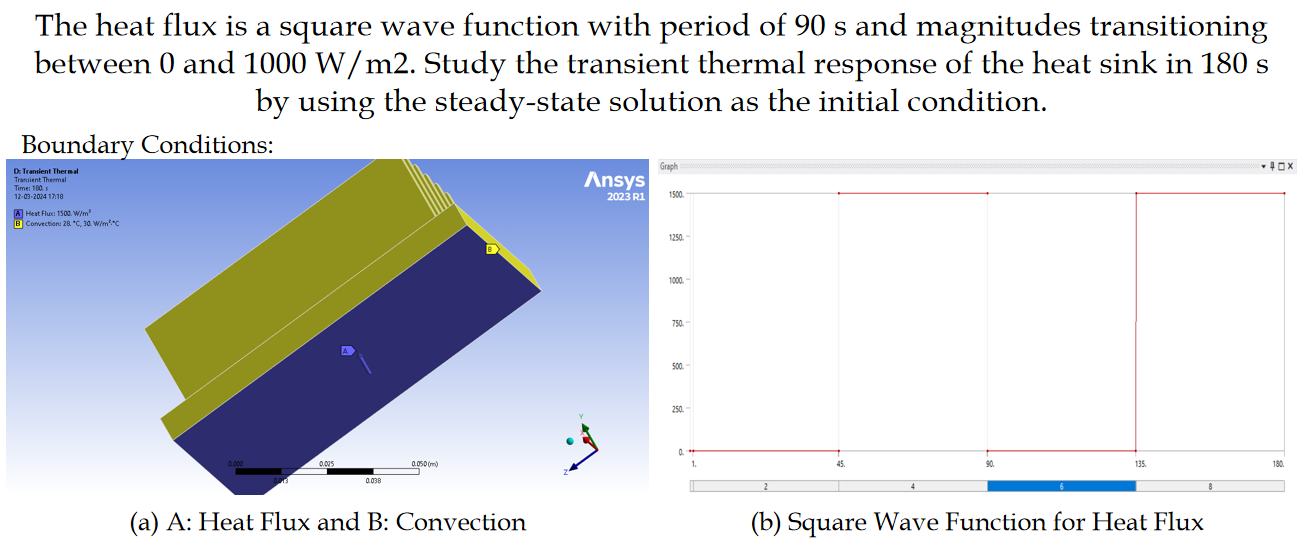
Results
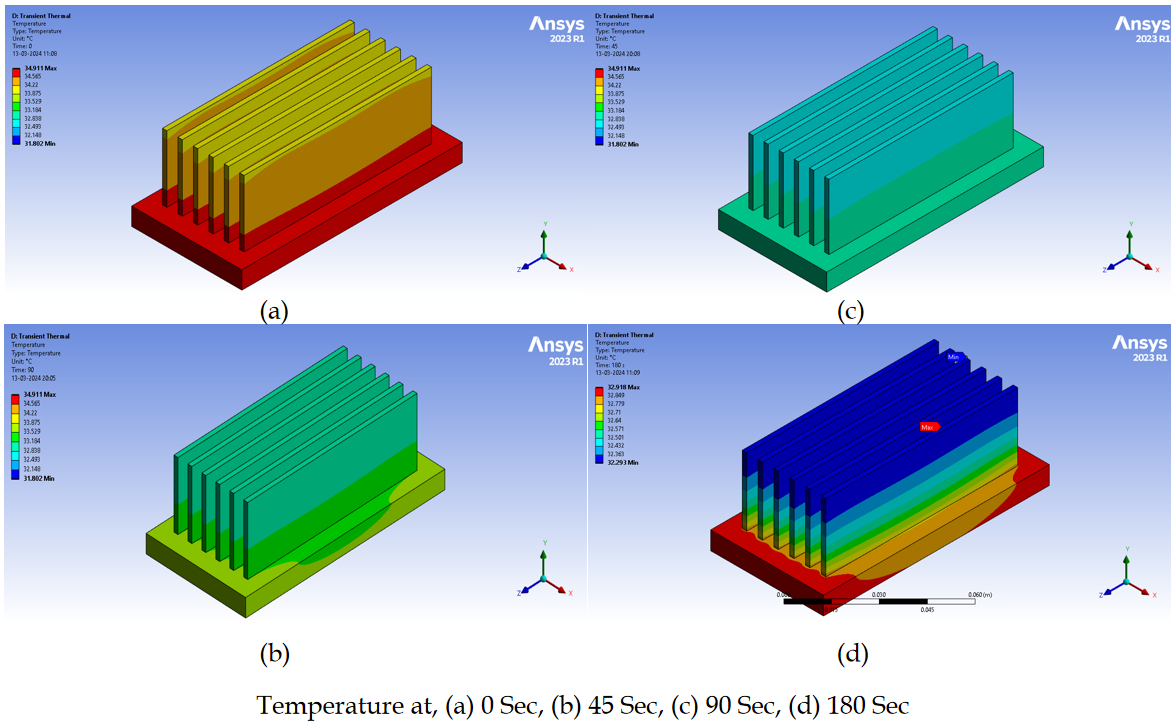
Conclusion
Rapid temperature response observed in CFD results reflects the heat sink's dynamic thermal adaptation capabilities.
Transient CFD analysis offers insights into the time-dependent thermal behavior essential for optimizing heat sink design.
CFD validation against transient conditions ensures accurate prediction of temperature fluctuations for real-world applications.
Task-3: Thermal Stress
Problem, Boundary conditions and Initial conditions
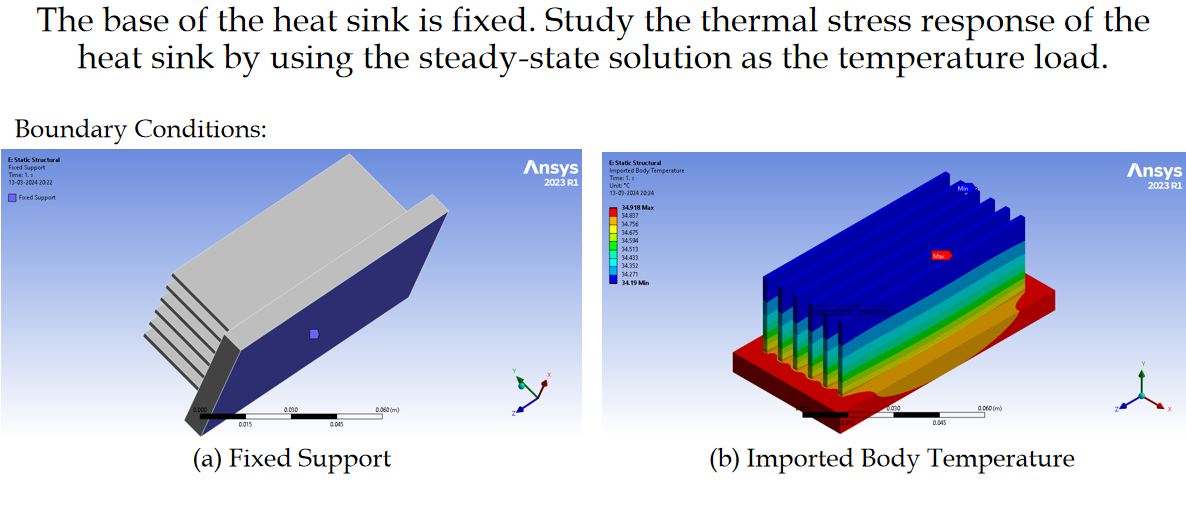
Results

Conclusion
Material properties such as Young’s modulus and Poisson’s ratio influence the generation and distribution of thermal stresses, as validated by CFD results.
Thermal expansion coefficients play a significant role in the development of thermal stresses within the heat sink structure.
Understanding thermal stress responses through CFD analysis aids in optimizing the heat sink design to mitigate potential structural failures and ensure long-term reliability.
Post a comment